Inthe ever-evolving landscape of pharmaceutical manufacturing, the quest forefficiency, sterility, and technological advancement has led industry leaderson a relentless pursuit of innovation. Among these pioneers, TRUKING hasemerged as a beacon of progress, particularly with the introduction of itsgroundbreaking Filtration, Washing, and Drying 3-IN-1 Machine. This developmentnot only underscores TRUKING's commitment to solving industry-wide challengesbut also sets a new benchmark for manufacturing excellence.
Identifyingthe Challenges
Historically,the pharmaceutical industry has grappled with several inefficiencies that havehampered production processes. Lengthy cleaning times, slow filtration rates,extended drying cycles, and low product yields have been persistent painpoints, along with the looming challenge of maintaining sterility. Moreover,the reliance on standalone machines has often precluded the realization of anintegrated solution to these issues.
TRUKING’sInnovative Response
In2021, TRUKING took a decisive step towards addressing these challenges byassembling a specialized team dedicated to research and development. Over twoyears, this team focused on creating a solution that could streamline themanufacturing process while ensuring high levels of efficiency and sterility.The result was the NFD - a state-of-the-art machine that encapsulatesfiltration, washing, drying, and automatic unloading in one compact unit. Its innovativesolution addresses several technical challenges in the industry by:
-
Enhancing filtration and washing efficiency:
-
Utilizing a multi-layer sintered mesh structure with a filtration pore size ≥1um.
-
Introducing metal sintered mesh laser automatic welding technology, reducing weld scars and achieving an effective filtration area of over 95%.
-
Offering an optional basket-style sintered mesh, improving filtration efficiency by 30%.
-
Customizable stirring types to increase washing efficiency.
Different stirring types
-
Improving drying efficiency:
-
The design includes a fully heated jacket structure for the tank body, base, and dust collector, covering over 90% of the area.
-
A full-cavity stirring paddle design increases the effective heating area by 60% compared to traditional paddles.
-
Utilizing jacket heating and vacuum drying, reducing drying cycles by 15% compared to traditional machines.
-
Increasing product yield:
-
An S-type stirring paddle with reverse rotation for automatic online unloading.
-
A 7mm ultra-narrow discharge valve design reduces residue significantly.
-
A gap of ≤4mm between the stirring paddle and filter, achieving a product yield of over 95%.
-
Sterile guarantees:
-
Inner tank mirror polishing with a roughness of Ra≤0.4 and 100% cleaning coverage.
-
Clean type mechanical seals and metal bellows with a Teflon seal structure for reliable sterile sealing.
-
A mechanically self-locking discharge valve maintains closure even during hydraulic pressure loss.
-
A closed sampling valve for online sampling.
-
Available for O-RABs and Isolator.
-
Intelligent control methods:
-
Fully automatic feeding, filtration, washing, drying, and discharging, with online CIP, SIP, and leak testing.
-
The control system is designed according to the ISA88 framework, meeting GAMP5 requirements.
-
Intelligent pre-maintenance functions for event and alarm notifications via email.
-
Integration with Siemens C/S or B/S architecture for centralized monitoring.
-
Comprehensive Solutions:
-
The machine can be paired with preparation system for sterile docking from the crystallization tank to the3-IN-1 machine.
-
Compatible with sterile isolation systems for Grade A environment sampling and unloading.
-
Can be integrated with TRUKING’s aluminum barrel cleaning, sterilization, filling, and capping line for a closed, fully automated sterile unlaoding process.
-
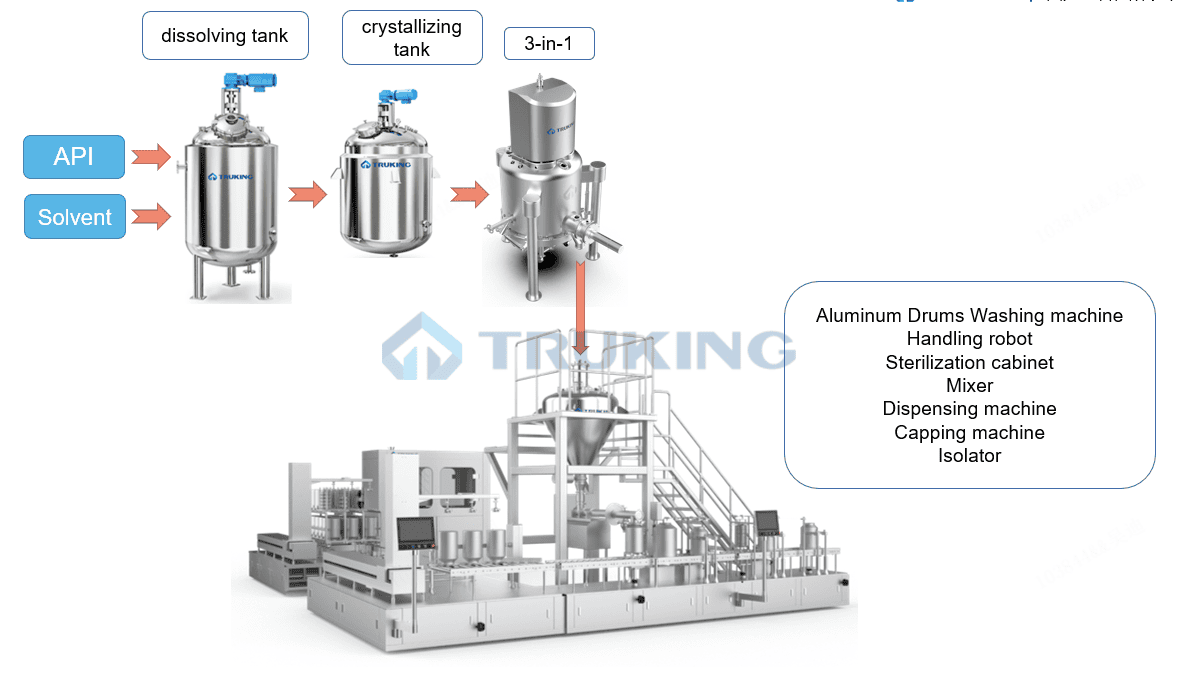